特靈公司使用OPTIMUS提升渦旋式風冷機組製冷劑管路疲勞壽命並縮短研發時間
傳統的研發流程中,研發團隊使用物理實驗和有限元素分析相結合的方式確保製冷劑管路的性能和品質,並以此方法解決可能導致產品可靠性降低的共振問題。但這種模式對於安裝了超過 100 條製冷劑管路的風冷機組而言,研發過程過於緩慢。特靈公司目前採用了一種新的自動化工作流模式,能夠在更短的時間內找到更好的設計方案。這種研發模式結合了實驗設計法、反應曲面模型法和最佳化演算法,通過自動修改製冷劑管路設計參數,以最高效的方式最小化其結構應力,並最佳化其他設計目標。這個自動化工作流透過 Optimus 結合 Ansys 軟體而實現。藉由評估 10 個設計方案,調整製冷劑管路的幾何形狀和尺寸,使得管路工作應力低於耐久極限要求,而這些工作都在傳統研發模式分析一個設計方案的時間內完成。
.bmp)
Optimus 整合 Ansys Workbench 之模擬工作流
渦旋式機組製冷劑管路的傳統設計流程,是透過有限元素模擬和物理實驗結合來實現的。首先用結構動力學有限元素法,預測單位運動幅度前提下所產生的應力大小。然後透過實驗,運行壓縮機確定管路的最大運動。因為要在不同運行速度下,對每條管路的所有共振峰值都進行激勵,所以這些實驗比較耗時。結合實驗中測出的管路運動和之前計算出的單位運動下管路的應力,就能預測出管路的真實應力水平。
如果應力超過了疲勞極限所允許的上限,管路就需要重新設計。通常的方式是通過增加製冷劑管路重量和降低管路剛度來降低管路的共振頻率。同樣,如果 要提高管路共振頻率,研發團隊就要設法降低管路質量和增加管路剛度。每次修 改設計方案,都要把之前的整個模擬和實驗過程重複做一遍。這是一個相當繁瑣 和耗時的過程,而且非常依賴工程師的經驗。
.bmp)
典型製冷劑管路 疲勞失效案例
特靈公司使用了 Noesis Solutions 公司的 Optimus 軟體。Optimus 是一款 整合了設計空間探索與數值最佳化方法的過程整合和設計最佳化軟體。Optimus 透過直接介面和 Ansys Workbench 無縫連接,能夠自動修改 Workbench 模型中的 設計參數,並且提取其計算結果。用戶只需把 Ansys Workbench 接口圖塊拖動到 Optimus 的工作流視窗中,就能實現 Ansys Workbench 的模擬工作流整合和自動 化,無須手動定義任何輸入輸出參數規則,也無須手動輸入腳本實現 Workbench 軟件調用。最終在 Optimus 的可視化工作流視窗中,通過對 Ansys Workbench 的直接介面,實現了參數化和自動化製冷劑管路模擬流程。
特靈公司的工程師建立了一個包含串聯渦旋壓縮機和製冷劑管路的 CAD 模 型,並把該模型導入 Ansys Workbench 中進行計算。工程師對製冷劑管路的主要 設計變量進行了參數化,並且定義了每個設計參數的合理取值範圍。然後他們把 模擬模型整合到 Optimus 中,實現自動化的模擬工作流,並在此基礎上進行了設 計空間探索和最佳化。
.bmp)
壓縮機框架和管路的 CAD 幾何模型 4 個載荷工況下的最大應力
在此基礎上,工程師使用Optimus在模擬工作流基礎上運行實驗設計(DOE), 用最小的計算量探索設計空間。在實驗設計樣本點上建立反應曲面模型,用於後 續快速尋找製冷劑管路的全域最佳設計方案。在該反應曲面模型上運行全域最佳 化演算法,無須運行任何 Ansys Workbench 模擬,極大地節省了最佳化時間。以 全域最佳化結果為起點,運行局部最佳化演算法,只需要幾次諧波響應計算就能 找到最終的最佳設計方案。Optimus 的自動化工作流和最佳化演算法最終找到製 冷劑管路一系列的最佳設計參數,確保管路局部交變應力小於 5000 psi。 新一代製冷機組設計複雜度的提升要求特靈工程師必須解決製冷劑管路設 計的強健性。特靈公司準備用 Optimus 驅動 Ansys 的最佳化流程應對這一挑戰, 在顯著降低每條管路應力的同時,確保其幾何和功能規格的一致性。公司下一步 的最佳化流程能夠在降低管路應力前提下確保其強健性,同時縮短產品的上市時 間。並且能夠釋放有限的研發資源,更有效地使用到更多項目上。
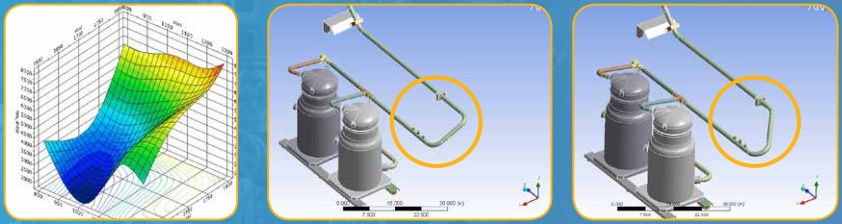
反應曲面模型3D圖 初始設計(左) 和最佳化設計(右)